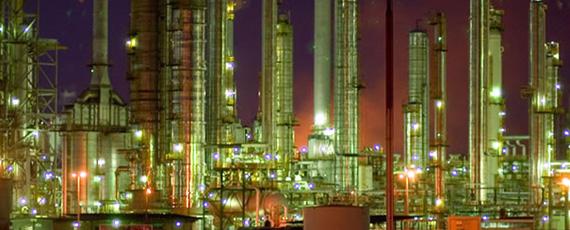
Petrochemical process lines require expansion joints to handle extreme pressures and operating temperatures up to 926 °C/1700 °F.
Design Considerations
The addition of expansion joints in a piping system introduces reaction forces produced by the expansion joint that must be taken into account when designing of the piping system.
How a Bellows Works
A bellows is a flexible seal. The convoluted portion of an expansion joint is designed to flex when thermal movements and/or vibrations occur in the piping system. The number of convolutions depends upon the amount of movement the bellows must accommodate or the force that must be used to accomplish this deflection. The convoluted element must be strong enough circumferentially to withstand the internal pressure of the system, yet responsive enough to flex. The longitudinal load (pressure thrust) must then be absorbed by some other type of device. These devices include pipe anchors, tie rods, hinges, or gimbal structures. Pressure thrust can be calculated by multiplying the effective area shown in the catalog by the working pressure.
Spring Force
Expansion joints behave in a manner that is similar to a spring; as movement occurs, expansion joints produce a resistive force. This resistance is stated as spring rate and measured as the force required deflecting the bellows 1” in the axial or lateral direction; or inch-lbs/degree for angular rotation. Spring force is the spring rate times the deflection.
Pressure Stresses
The ability of a bellows to carry pressure is limited by hoop stress or S2 as defined in the standards of the Expansion Joint Manufacturers Association (EJMA). This is a stress that runs circumferentially around the bellows due to the pressure difference between the inside and the outside of the bellows. Hoop stress is what holds a bellows together like the hoops on a barrel. This stress must be held to a code stress level. The customer should specify the code to be used. The bellow’s ability to carry pressure is also limited by bulge stress or EJMA stress S4. This is a stress that runs longitudinal to the bellows centerline. More specifically, it is located in the bellows sidewall and it is a measure of the tendency of the convolutions to become less U-shaped and more spherical.
For bellows that are not annealed after forming, S4 is allowed by EJMA to exceed the initial yield strength of the bellows material by a large margin because it is cold worked. If a bellows is annealed after forming, S4 must be severely limited because the bellows sidewall material is no longer cold worked.
Accommodating a requirement for annealing will often result in the addition of reinforcing rings or a much heavier bellows material and more convolutions. PisaFlex’s standard policy is to provide bellows in the as-formed condition to take advantage of the added performance that is imparted to the bellows through cold work. We will accommodate annealing requirements on request.